Supply Chain Optimization
Streamlined supply chain operations, automated inventory tracking and improved communication between suppliers, warehouses and customers to enhance efficiency and reduce operational delays.
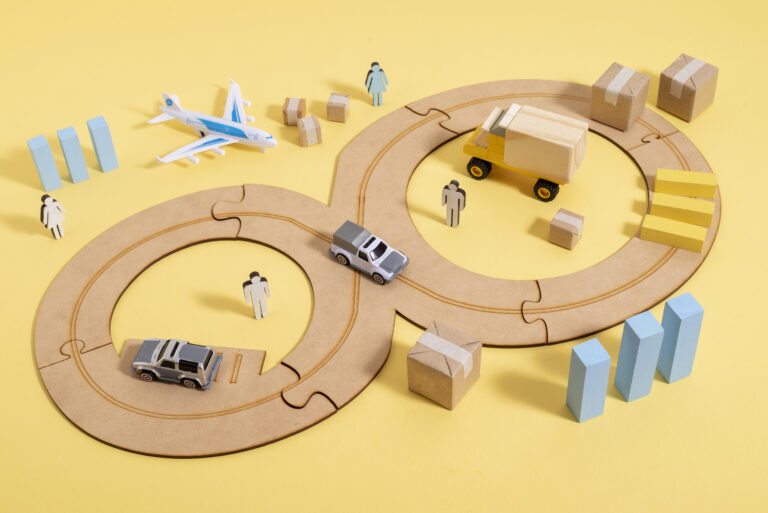
About GDI Supply Chain Automation
Glob Distributors Inc. is a leading distributor of industrial equipment and machinery parts, serving a wide range of industries including manufacturing, construction, and logistics. With a global supply network, the company handles thousands of shipments daily, managing complex workflows across procurement, inventory, and order fulfillment. As the business grew, so did the complexity of their supply chain processes, leading to inefficiencies, delays, and higher operational costs.
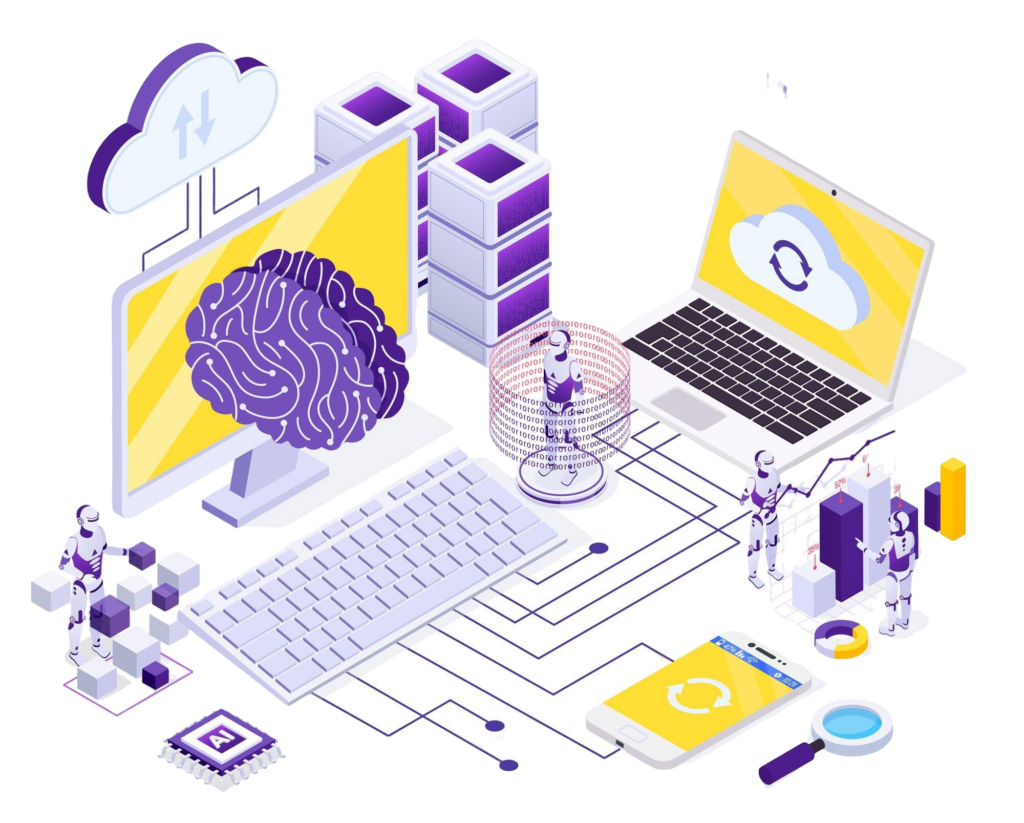
The challenge
Glob Distributors faced several critical challenges:
- Manual Order Management: The company relied on manual data entry for inventory updates, purchase orders, and shipment tracking, which resulted in delays and inaccuracies.
- Disjointed Systems: Multiple systems for procurement, inventory, and logistics management were not integrated, causing communication gaps and delays between suppliers, warehouses, and customers.
- Inventory Visibility Issues: Lack of real-time inventory tracking led to frequent stockouts and overstocking, disrupting the order fulfillment process and increasing costs.
These inefficiencies resulted in increased lead times, higher operational costs, and lower customer satisfaction.
Services Rendered:
STRENGTH IN NUMBERS
Business impact
Global Distributors implemented a custom automation solution that automated and integrated key supply chain processes for optimized workflows, resulting in:
Hours saved/ month
Inventory Accuracy
Increase fulfilment efficiency
Custom automation solutions
The iPaaS platform used in this case was Workato, which seamlessly integrated SAP ERP, Shopify for e-commerce, and ShipBob for fulfillment management. The platform enabled the automation of workflows across procurement, inventory management, and order fulfillment, ensuring data consistency across all systems.
Significant improvements in operational efficiency, inventory accuracy, and customer satisfaction, along with cost savings.
- The automated order processing and inventory updates saved manual efforts.
- Real-time inventory synchronization led to significant inventory accuracy rate, drastically reducing stockouts and overstocking incidents.
- Streamlined communication and faster order fulfillment resulted in improvement in customer satisfaction scores.
+30 %
Reduced operational costs
22 %
Improved lead time
41 %
Increase in net order volume